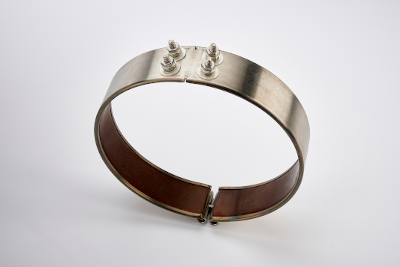
How to Configure a Band Heater
While readily available, stock band heaters can sometimes fall short in meeting the specific demands of unique or complex applications. Customized band heaters are designed to fit an application’s exact dimensions and heating requirements to ensure optimal heat distribution, energy efficiency, and precise temperature management.
Multiple factors of a band heater can be customized. In this article, our experts at Hi-Watt will guide you through using our configurator to customize your band heater.
Type
You can choose from two primary types of band heaters: mica or ceramic.
Mica

Mica heaters are generally less expensive. However, they can only withstand temperatures up to 900 degrees Fahrenheit (480 degrees Celsius), so they are not well-suited for high-temperature applications. Mica band heaters are typically used in plastic injection molding machines, blow molding machines, and other plastics machinery.
Ceramic
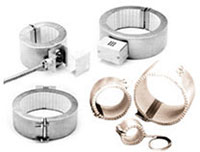
Ceramic heaters are better suited for high-temperature applications, as they can withstand temperatures up to 1,200 degrees Fahrenheit (650 degrees Celsius). It also insulates better than mica. The downside is that they’re generally more expensive and more rigid, which can limit their application in terms of fit and size customization.
Construction
Next, you’ll pick a construction option. There are three you can choose from: standard, expandable, and 2PC (two-piece). Your chosen construction type will vary based on your application.
Standard
Standard heaters are single-piece constructions that wrap around the component being heated. They are simple and suitable for applications where the heater needs to be easily slid over the part. However, they are difficult to install in confined spaces.
Expandable
Expandable heaters are flexible, so they’re especially useful when you can’t simply slide the heater over an object. They are designed to expand to fit over the part and then contract for a snug fit. Unlike standard heaters, expandable heaters are recommended for tight spaces. They’re also good for retrofitting machinery because they require no disassembly. The downside of expandable heaters is that they may require more careful handling during installation to prevent damage.
2PC
Two-piece heaters are designed to open up and fit around the part. They’re easier to install on parts with complex geometries, don’t require part disassembly, and are well-suited for objects that aren’t easily accessible. Be cautious when installing two-piece band heaters because there is a higher potential for misalignment.
Diameter
A correctly sized diameter helps ensure the heater fits snugly around the component it’s intended to heat, reduces energy wastage, and improves the uniformity of heat distribution.
To figure out your diameter, you’ll need to measure the outer diameter of the component that will be heated. Be precise with your measurements because you need an exact match. A heater that is too large won’t make sufficient contact, resulting in poor heat transfer, while one that’s too small will be too difficult to install and cause damage to both the heater and the component it’s heating.
Voltage Requirements
To prevent electrical overloads, you’ll need to determine the correct voltage for your band heater by identifying the voltage capacity of the power source where the heater will be connected. Most industrial band heaters are 480V. However, it’s still important to check the specifications of your facility’s electrical system or the machinery that the heater will be attached to.
Target Wattage
The target wattage determines how much power the heater uses to generate heat, and how quickly and effectively the band heater can heat an object.
Determining the wattage can be challenging because it requires knowledge of the material properties of the object being heated, the desired temperature increase, and ambient conditions. If you don’t know your target wattage, please contact Hi-Watt’s application specialists at (955) 467-5628 for assistance.
Clamping Option
The clamping option you choose will vary based on your environmental conditions, required heating uniformity, and ease of installation or removal.
There are generally four options: straps, flange lock-up, welded-on barrel nuts, and spring-loaded barrel nuts.
Straps
Straps are adjustable, typically made of metal, and can be easily adjusted with a screw or bolt. They’re easy to install and work well in less-demanding applications, but they may not provide as tight a fit as other options.
Flange Lock-up
This clamping option involves bolting the flange directly to the machinery or component being heated. It’s also ideal for very narrow band heaters because it allows the heater to maintain proper contact with the machinery or component it’s intended to heat without any slipping or misalignment. The flange-lock up design also helps maintain consistent contact along the entire length of the heater, which is particularly important for narrow configurations.
Welded-on Barrel Nuts
Welded-on clamping allows bolts to pass through and secure the band heater tightly against an object, ensuring consistent heating and safety in high-temperature applications.
This clamping option is particularly useful for band heaters that have holes or cut-outs because they minimize the risk of the heater shifting or loosening. Additionally, unlike straps, which may need to wrap around the entire circumference of the heater, welded-on barrel nuts don’t interfere with any holes or cut-outs on the band heater. Straps can potentially cover or press against these cut-outs, obstructing functionality or leading to uneven heating distribution.
Welded-on barrel nuts are not suited for applications requiring flexibility, as removing or adjusting the heater after it’s been clamped can be more challenging and time-consuming.
Spring-Loaded Barrel Nuts
If your application has significant temperature variations, this clamping option is the better choice. It incorporates a spring mechanism that maintains constant tension on the clamping nuts, compensating for the heater’s expansion and contraction due to temperature fluctuations.
Termination
Your termination type should align with your application’s connectivity needs, operational environment, and maintenance requirements.
We provide three termination options: leads, post terminals, and euro plugs.
Leads
Leads are insulated wires extending from the heater. They are best suited for applications where the heater needs to be connected at a distance or where direct access is limited. They can vary in length and insulation type, making them ideal for high-temperature applications or harsh environments. Leads are useful because they can be routed through complex machinery layouts where direct connections aren’t feasible. The downside is that exposed leads may be susceptible to damage from abrasion or chemical exposure unless protected.
Post Terminals
Post terminals are bolted connections typically used in environments where a strong connection is needed. They are also easier to inspect and maintain than embedded or sealed connections, so they’re ideal for industrial environments where frequent maintenance checks are needed. Similar to leads, post terminals can be susceptible to moisture or dust if not properly protected.
Euro Plugs
Euro plugs are quick-connect terminals that make connection fast and easy. They’re more compact than leads, but they’re not suitable for high temperatures or extremely harsh environments. They’re best used for applications requiring frequent heater changes (since they are easy to install) or where downtime needs to be minimized, like in manufacturing processes with varying temperature requirements.
Length & Material
Next, determine how long the terminal should be. Measure the distance from the heater’s installation point to the power connection point and choose a length that can span this distance without straining the wires or connectors. You also want to prevent tangling or excessively loose wires, which can be safety hazards.
Selecting a terminal material requires evaluating the operational environment (high-temp, corrosive, etc.) and electrical requirements.
For example, nickel-plated brass works well in high-temperature environments, while stainless steel will provide exceptional reliability in highly corrosive environments.
Our application specialists can help you select the best material for your terminals.
Ground Wire
Ground wires are needed in conductive environments to prevent electrical shocks and reduce fire risks.
Terminal Box
If your band heater will be in a hazardous environment, used in an outdoor application, or placed in a high-traffic area, you should consider a terminal box. This optional accessory protects your band heater (and its electrical connections) from dust, moisture, and chemical vapors, prevents accidental contact, and helps manage and organize the wiring.
Thermocouple
A thermocouple is an ideal add-on to your band heater if you need continuous, real-time temperature measurements or automatic power output adjustments. Common applications requiring a thermocouple include injection molding, semiconductor manufacturing, metal processing, and chemical processing.
Holes
Mounting/fastening holes are needed:
- When applications require a permanent or semi-permanent installation.
- In environments where the heater will be exposed to excessive movement or vibration.
- In higher-traffic areas, where there’s a risk of workers accidentally coming into contact with the heater.
If you need mounting holes for your heater, our application specialists can help you determine their location and size.
Other Customization Options/Special Requests
There are other special requests you could ask for when configuring your band heater, including:
- Built-in insulation for better thermal efficiency.
- Ceramic insulation for high-temperature applications.
- Corrosion- or moisture-resistant coatings for chemically aggressive or high humidity environments.
- Flat profiles for surface heating.
- Custom-shaped profiles for non-standard part geometries.
- Segmented heating for complex processes.
- Reflective backing to direct more heat onto a part.
Configure Your Band Heater Today
There are many variables to consider when customizing a band heater—if you’re still not sure where to start or what you need, Hi-Watt is here to help. You can fill out our online form or call (855) 467-5628 today to speak with one of our application specialists.